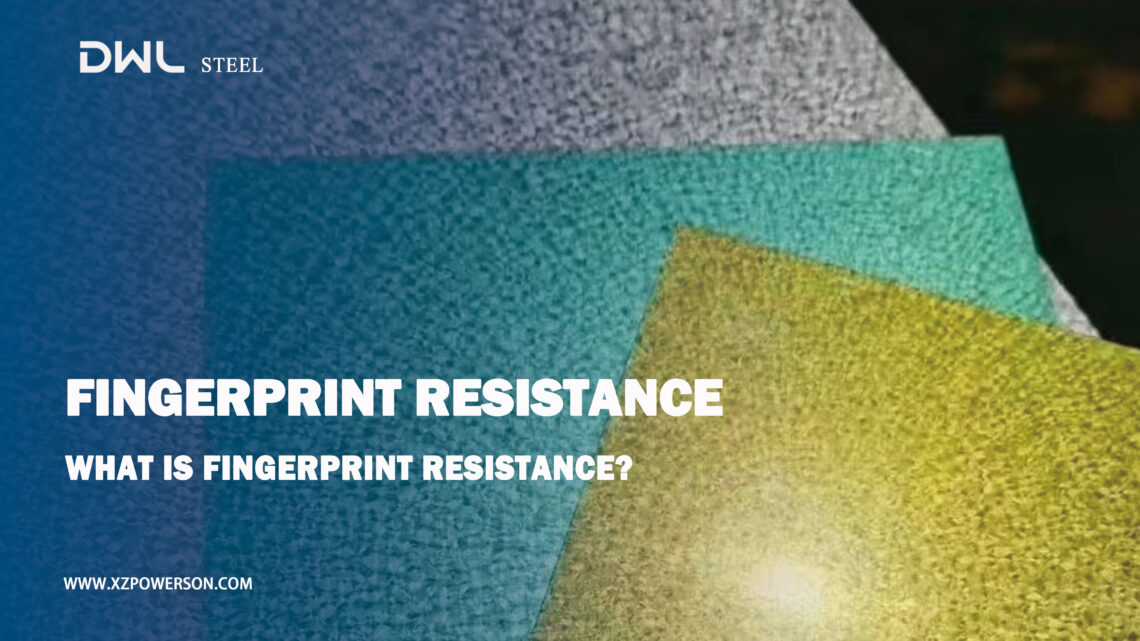
What is Fingerprint Resistance?
Fingerprint Resistance Treatment:
Fingerprint resistance treatment refers to the process of chemically and electrochemically treating the surface of metal plates to endow the galvanized layer with fingerprint resistance and a certain degree of corrosion resistance.
1. Research Approach for Fingerprint Resistance: People aim to eliminate the impact of fingerprints by treating galvanized steel sheets so that they do not transfer or adhere to fingerprints, maintaining a “non-stick” state on the steel surface. However, current technology struggles to achieve complete “non-stick” properties. Since the 1980s, research has focused on finding substances with optical characteristics similar to human fingerprints and pre-coating them on the steel surface. This way, even if fingerprints adhere, the optical reflection difference between the adhered and non-adhered areas is minimal, thereby achieving fingerprint resistance. Broadly speaking, fingerprint resistance is a form of anti-pollution capability. Research has revealed that the challenge lies in enhancing the corrosion resistance of steel plates while maintaining their fingerprint resistance, comparable to chromate passivation.
2. Classification of Fingerprint Resistant Coated Sheets: Organic coated steel sheets are a new type of composite metal material formed by applying various organic coatings on bare or coated steel sheets. First developed in the United States in the 1930s, organic coated steel sheets rapidly evolved in the 1950s, primarily for building materials applications. In recent years, as users have demanded higher corrosion resistance from galvanized steel sheets, these sheets have also been used to provide rich colors on external components. The performance of organic coated steel sheets varies based on the type, color, or thickness of the coating. Depending on the coating thickness and application, they can be categorized into thick-coated and thin-coated organic coated steel sheets. Thick-coated types generally have an organic coating thickness of over 15μm, while thin-coated types have a thickness of less than 5μm. Fingerprint-resistant organic coated steel sheets belong to the thin-coated category.
3. Development History of Fingerprint Resistance Treatment: The development of fingerprint resistance treatments has progressed through two stages based on the chemical nature of the coating: inorganic series films and organic series films. Organic series films can further be divided into traditional organic series films and eco-friendly organic series films.
• 3.1 Inorganic Series Films: Early fingerprint resistance treatments involved forming an inorganic series film, typically a silicate film, on top of a chromate-passivated zinc-coated steel sheet. This process can be achieved using electrolytic coating methods. By adjusting the concentration of hexavalent chromium and trivalent chromium ions in the electrolyte solution, controlling the pH value and temperature, a composite coating with excellent corrosion resistance and fingerprint resistance can be formed. Silica dioxide is often added to the treatment solution to form an inorganic salt film series. Kobe Steel Company (Japan) pioneered the “Kobe Electro-Galvanized K Treatment,” which forms a silicate film on top of a chromate-passivated film. This inorganic series steel was widely used by many home appliance manufacturers for products like VCR bases, audio equipment, and induction cooker base plates. Due to its conductivity, it was also used in computer casings. However, while inorganic series fingerprint-resistant films offer short-term rust prevention under mild conditions, their long-term corrosion resistance in harsh environments is insufficient. Additionally, their conductivity is relatively poor.
• 3.2 Organic Series Films: With increasing product diversification, users now demand higher requirements for fingerprint-resistant boards, including grounding properties, higher corrosion resistance, and better painting performance. Thin-film organic composite coatings on chromate-passivated galvanized steel sheets were thus developed. Organic-type fingerprint-resistant steel sheets offer better corrosion resistance and grounding properties compared to inorganic types but have slightly lower fingerprint resistance. Both types meet the corrosion resistance requirements of the home appliance industry. Traditional organic fingerprint-resistant treatment processes, often called chromate-based organic composite thin coatings, can be applied in two main ways:
• Two-Step Method: After passivating the galvanized steel sheet, an organic coating (fingerprint-resistant film) is applied over the passivated film, mainly using roll coating.
• One-Step Method: Organic resins and/or colloidal silica are added to the passivation solution for galvanized steel. After passing through the passivation tank, a composite coating with corrosion and fingerprint resistance is formed on the surface, mainly using electrolytic coating or roll coating. Traditional organic fingerprint-resistant solutions typically consist of base resins and colloidal silica. Different base resins, such as polyethylene, acrylic, epoxy, and polyurethane, affect the drying temperature of the organic film. Colloidal silica enhances the strength and corrosion resistance of the organic coating when added to the resin. For higher fingerprint resistance requirements, the two-step method is generally preferred. The presence of the organic coating acts as a barrier, significantly improving the corrosion resistance of the coated steel sheet. Kawasaki Steel Corporation’s Chiba plant developed the “River Zinc F” fingerprint-resistant board, which uses a colloidal silica-containing alkyd resin and roller coating for application. The organic resin layer dries at a lower temperature to prevent aging and adverse effects on the chromate-passivated film.
Studies have shown:
• Selecting water-based resins for safety and operational convenience.
• Adding colloidal silica improves corrosion resistance; optimal results are achieved with a silica content of 10-15%.
• Coating weight significantly affects corrosion and fingerprint resistance. A coating weight of 0.3-1.0g/m² offers the best overall performance.
• 3.3 Eco-Friendly Organic Series Films: In developed countries, environmental concerns have led to the gradual adoption of chromium-free passivators in steel production. These organic composite coatings integrate multiple properties, aiming to satisfy various usage requirements simultaneously, such as fingerprint resistance, conductivity, self-lubrication, and paintability. This type of organic composite coating is rapidly developing and has become the mainstream. Hicharm USA has developed a chromium-free organic coating with equivalent corrosion resistance to chromium-containing coatings. These coated sheets possess excellent fingerprint resistance, conductivity, and paintability, meeting high forming performance, high coating hardness, and self-lubrication during stamping deformation, suitable for internal parts of home appliances, audio equipment, personal computers, and copier components. Eco-friendly organic series films represent the mainstream of modern fingerprint resistance treatment and remain a key research focus. Their primary components typically include passivation liquids, silica, resins, waxes, and additives. The critical technology in eco-friendly organic series film processing lies in selecting chromium-free passivation liquids. Modern chromium-free fingerprint resistance treatments have developed various types, no longer limited to traditional acidic systems, allowing for passivation film formation under alkaline conditions.
4. Research Directions for Fingerprint Resistance:
• 4.1 Base Material for Fingerprint Resistance Treatment: Initially, galvanized steel sheets were the primary base material for fingerprint-resistant coatings. As technology and processes improve, more base materials, such as hot-dip galvanized steel, aluminum-zinc alloy sheets, aluminum sheets, and stainless steel sheets, are being used. Hot-dip galvanized steel, in particular, has achieved surface quality comparable to electrogalvanized steel, offering better corrosion resistance at a lower cost, making it the mainstream base material for fingerprint resistance.
• 4.2 Eco-Friendly Fingerprint Resistance Treatment: Research and development will continue to focus on chromium-free fingerprint resistance treatments, aiming to develop coatings with self-healing capabilities and excellent corrosion, alkali, solvent, and fingerprint resistance.
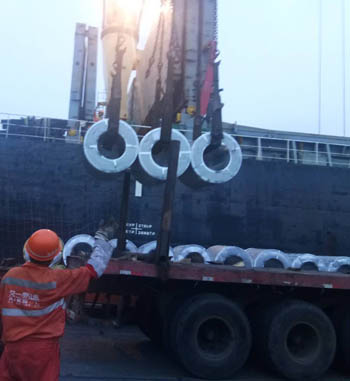
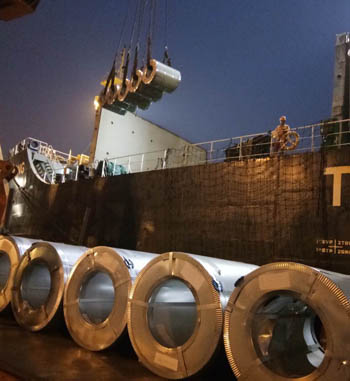
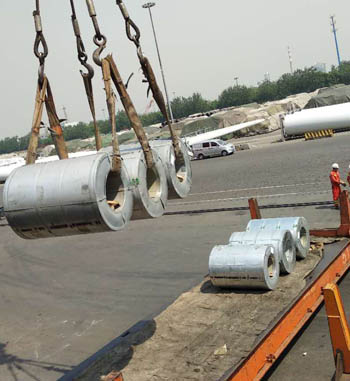
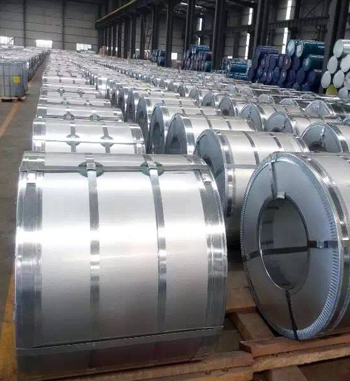
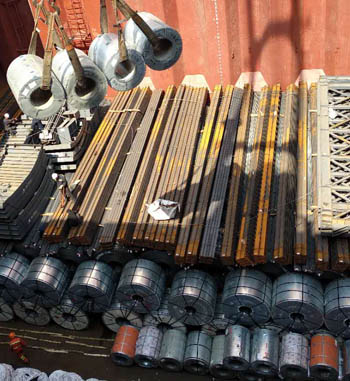
PROFESSIONAL TEAM
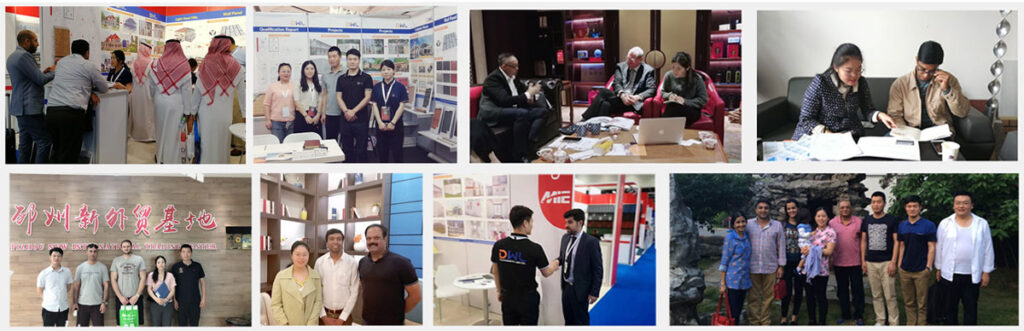
Related Products
21 years steel export experience for Color Coated PPGI