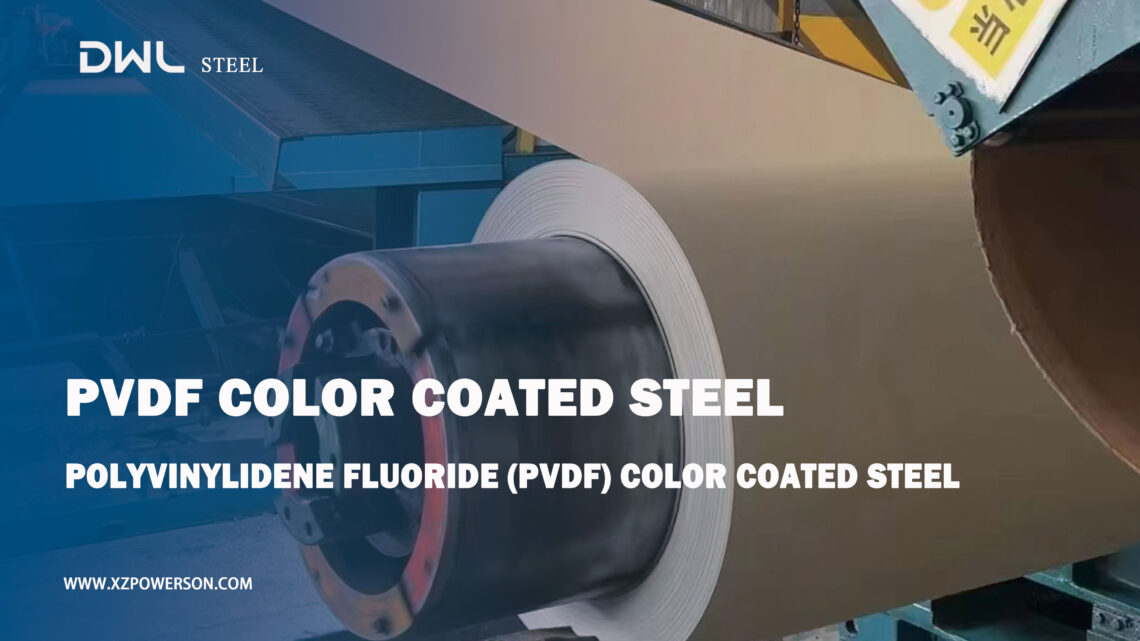
Polyvinylidene Fluoride Color Coated Steel
Polyvinylidene Fluoride (PVDF) coated steel sheets stand as a high-tech product in modern building materials, distinguished by their exceptional weather resistance, chemical corrosion resistance, and outstanding mechanical properties, thereby showcasing unparalleled application value across various sectors. This discussion delves into the intricacies of PVDF coated sheets, covering fundamental concepts, unique advantages, manufacturing processes, primary applications, and market trends.
Basic Concept
PVDF coated sheets are a type of high-performance composite material fabricated by evenly applying a coating made from PVDF resin mixed with pigments, additives onto metal substrates such as galvanized steel or aluminum panels, followed by high-temperature baking for curing. The fluorocarbon bond structure inherent in PVDF resin imparts the coating with remarkable stability, effectively resisting environmental erosion.
Unique Advantages
1.
Exceptional Weather Resistance: PVDF coatings boast extended outdoor durability, enduring extreme climatic conditions including intense UV radiation and weather erosion. They maintain colorfastness for over 20 years, surpassing ordinary coating materials by a substantial margin.
2.
Excellent Chemical Corrosion Resistance: In harsh chemical environments like acid rain and salt spray, PVDF coated sheets demonstrate superior resilience, making them particularly suitable for applications in coastal areas and chemical plants.
3.
Superior Mechanical Properties: With an optimal balance between hardness and toughness, they possess high impact resistance and do not crack easily during bending, providing robust protection to building structures.
4.
Self-Cleaning Property: The unique structure of PVDF coatings results in low surface energy, enabling rainwater to wash away most dust and dirt, thus reducing maintenance costs.
5.
Environmental Safety: PVDF materials are non-toxic, non-flammable, and environmentally friendly during production and use, aligning with the current trend of green building development.
Manufacturing Process
The production of PVDF coated sheets involves substrate pretreatment, paint formulation, coating, and baking curing. Initially, metal substrates undergo rigorous cleaning, degreasing, and chemical conversion treatment to ensure good adhesion of the coating. Subsequently, PVDF resin is mixed with other components in precise ratios to formulate the paint, which is then uniformly applied to the substrate using precision equipment. Finally, the sheets are cured in a high-temperature oven to achieve full cross-linking, forming a durable surface.
Primary Application Fields
1.
Architectural Design: Used as curtain walls, roofing, and interior decoration panels, especially in landmark buildings, sports stadiums, airports, where they exhibit both aesthetic and practical value.
2.
Industrial Facilities: As protective panels for equipment and exterior pipes in corrosive environments like chemical plants and power plants, significantly prolonging facility lifespan.
3.
Transportation Infrastructure: Interior and exterior decorative panels for subways, high-speed trains, offering both aesthetics and resistance against wind pressure and wear at high speeds.
4.
Household Appliances: Casings for refrigerators, air conditioners, providing excellent scratch and weather resistance.
Market Trends & Outlook
With the popularization of energy-saving buildings and green building concepts, alongside heightened requirements for material durability and eco-friendliness, the PVDF coated sheet market is experiencing rapid growth. Technological innovations, including more eco-friendly production techniques and the development of higher performance PVDF formulations, will further expand its application scope. It is anticipated that PVDF coated sheets will continue to unveil their unique appeal in emerging sectors in the future.
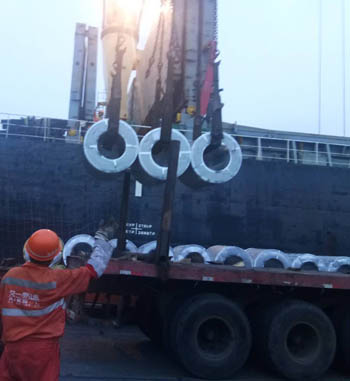
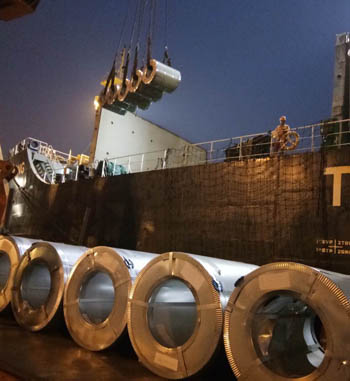
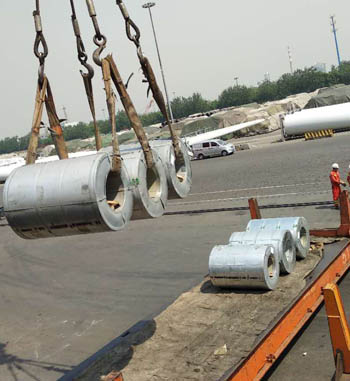
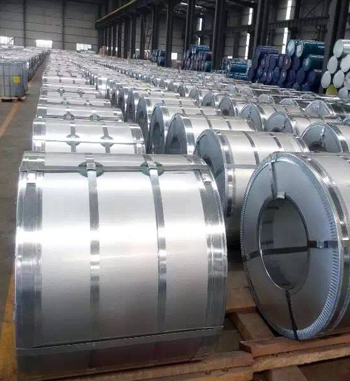
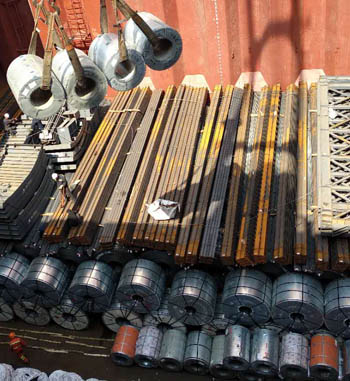
PROFESSIONAL TEAM
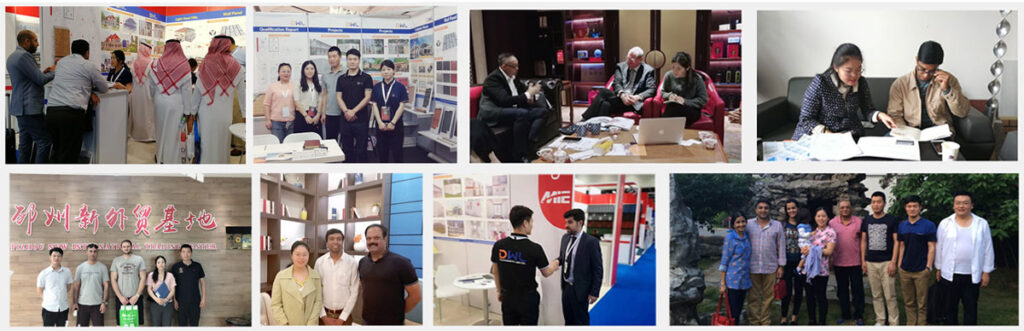
Related Products
21 years steel export experience for Color Coated Steel