Analysis of Defects Caused by Missed Galvanization in Galvanized Steel Sheets
2024年11月4日 关 作者 powerson metal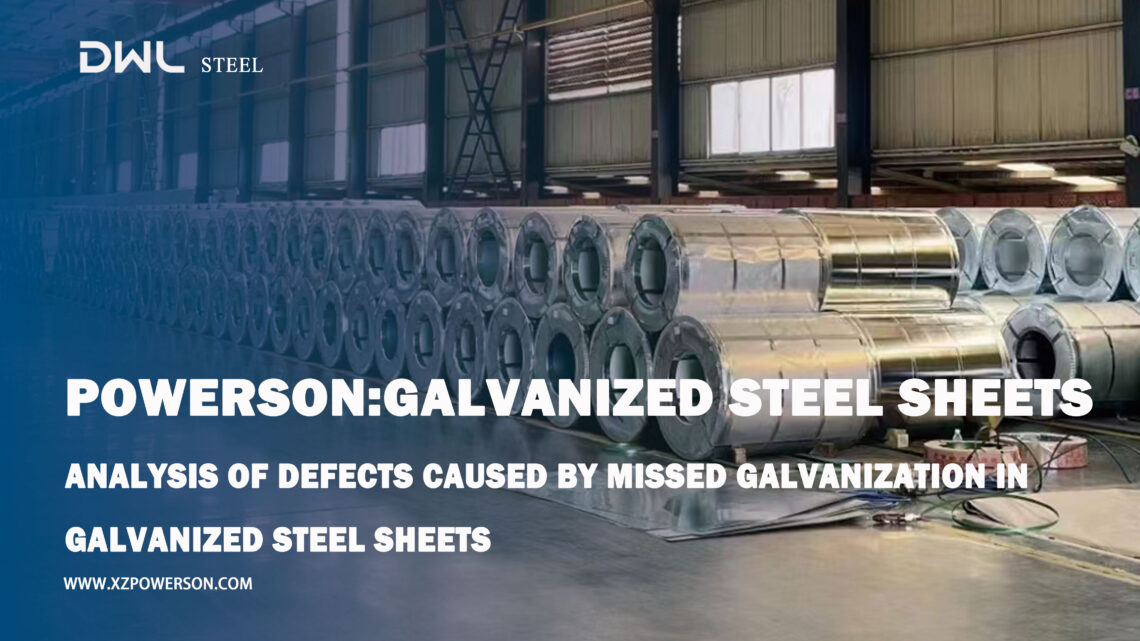
Analysis of Defects Caused by Missed Galvanization in Galvanized Steel Sheets
- Afrikaans
- Albanian – shqipe
- Arabic – العربية
- Armenian – Հայերէն
- Azerbaijani – azərbaycanca
- Basque – euskara
- Belarusian – беларуская
- Bengali – বাংলা
- Bulgarian – български
- Catalan – català
- Chinese – 中文(简体中文)
- Chinese – 中文 (繁體中文)
- Croatian – hrvatski
- Czech – čeština
- Danish – dansk
- Dutch – Nederlands
- English
- Esperanto – esperanto
- Estonian – eesti
- Filipino
- Finnish – suomi
- French – français
- Galician – galego
- Georgian – ქართული
- German – Deutsch
- Greek – Ελληνικά
- Gujarati – ગુજરાતી
- Haitian Creole – kreyòl ayisyen
- Hebrew – עברית
- Hindi – हिन्दी
- Hungarian – magyar
- Icelandic – íslenska
- Indonesian – Bahasa Indonesia
- Irish – Gaeilge
- Italian – italiano
- Japanese – 日本語
- Kannada – ಕನ್ನಡ
- Korean – 한국어
- Latin – Lingua Latina
- Latvian – latviešu
- Lithuanian – lietuvių
- Macedonian – македонски
- Malay – Bahasa Melayu
- Maltese – Malti
- Norwegian – norsk
- Persian – فارسی
- Polish – polski
- Portuguese – português
- Romanian – română
- Russian – русский
- Serbian – Српски
- Slovak – slovenčina
- Slovenian – slovenščina
- Spanish – español
- Swahili – Kiswahili
- Swedish – svenska
- Tamil – தமிழ்
- Telugu – తెలుగు
- Thai – ไทย
- Turkish – Türkçe
- Ukrainian – українська
- Urdu – اردو
- Vietnamese – Tiếng Việt
- Welsh – Cymraeg
- Yiddish – יידיש
Double-click
Select to translate
Galvanized steel sheets are widely used in various industries due to their excellent corrosion resistance, durability, and cost-effectiveness. However, one of the most common defects that can occur during the galvanization process is missed galvanization, also known as “missed spots” or “bare spots.” These defects can significantly reduce the corrosion resistance and overall quality of the galvanized steel sheets. This article will delve into the causes of missed galvanization and provide insights into how these issues can be mitigated.
1. Introduction to Missed Galvanization
Missed galvanization refers to areas on the surface of a galvanized steel sheet where the zinc coating is absent or insufficient. These bare spots are highly susceptible to corrosion and can compromise the integrity and longevity of the steel sheet. Understanding the root causes of missed galvanization is crucial for improving the quality and reliability of galvanized steel products.
2. Causes of Missed Galvanization
2.1 Surface Contamination
One of the primary causes of missed galvanization is surface contamination. Any foreign substances on the surface of the steel sheet, such as oil, grease, dirt, or oxide scale, can prevent the zinc from adhering properly. Proper cleaning and pretreatment of the steel sheet before galvanization are essential to remove these contaminants.
2.2 Inadequate Pretreatment
Pretreatment processes, such as degreasing, pickling, and rinsing, are critical steps in preparing the steel sheet for galvanization. If any of these steps are not performed correctly, it can lead to missed galvanization. For example, insufficient degreasing can leave residual oils on the surface, while inadequate pickling may not fully remove the oxide scale.
2.3 Poor Zinc Bath Management
The quality and condition of the zinc bath play a significant role in the galvanization process. Factors such as temperature, composition, and impurities in the zinc bath can affect the adhesion and uniformity of the zinc coating. A poorly maintained zinc bath can result in missed galvanization.
2.4 Mechanical Issues
Mechanical issues during the galvanization process can also cause missed galvanization. For instance, if the steel sheet is not properly aligned or positioned in the zinc bath, certain areas may not receive adequate zinc coverage. Similarly, equipment malfunctions or improper handling can lead to bare spots.
2.5 Chemical Composition of Steel
The chemical composition of the steel sheet itself can influence the galvanization process. Certain elements, such as silicon and phosphorus, can affect the reactivity of the steel with the zinc bath. High levels of these elements can lead to uneven zinc deposition and missed galvanization.
2.6 Rapid Cooling
Rapid cooling of the galvanized steel sheet after immersion in the zinc bath can sometimes cause missed galvanization. Rapid cooling can lead to the formation of a brittle intermetallic layer between the zinc and steel, which can result in poor adhesion and bare spots.
3. Mitigation Strategies
To minimize the occurrence of missed galvanization, several mitigation strategies can be employed:
3.1 Enhanced Surface Preparation
Thorough and consistent surface preparation is essential. This includes rigorous cleaning, degreasing, and pickling processes to ensure that the steel sheet is free from contaminants before galvanization.
3.2 Optimal Zinc Bath Management
Maintaining the zinc bath at the correct temperature and composition is crucial. Regular monitoring and adjustment of the bath parameters can help ensure uniform and complete zinc coverage.
3.3 Proper Equipment Maintenance
Regular maintenance and calibration of the galvanization equipment can prevent mechanical issues that may cause missed galvanization. Ensuring that the equipment is functioning optimally is key to achieving high-quality galvanized steel sheets.
3.4 Controlled Cooling
Controlling the cooling rate of the galvanized steel sheet can help prevent the formation of a brittle intermetallic layer. Gradual cooling processes can improve the adhesion of the zinc coating.
3.5 Selection of Appropriate Steel Grades
Choosing steel grades with a balanced chemical composition can reduce the risk of missed galvanization. Steel with lower levels of silicon and phosphorus is generally more suitable for galvanization.
4. Conclusion
Missed galvanization is a significant defect that can severely impact the performance and longevity of galvanized steel sheets. By understanding the causes of this issue and implementing effective mitigation strategies, manufacturers can produce high-quality galvanized steel sheets that meet the stringent requirements of various industries. Proper surface preparation, optimal zinc bath management, regular equipment maintenance, controlled cooling, and the selection of appropriate steel grades are all critical factors in ensuring the success of the galvanization process.
This comprehensive approach not only enhances the quality of galvanized steel sheets but also reduces production costs and improves customer satisfaction. By addressing the root causes of missed galvanization, the galvanization industry can continue to deliver reliable and durable products that stand the test of time.