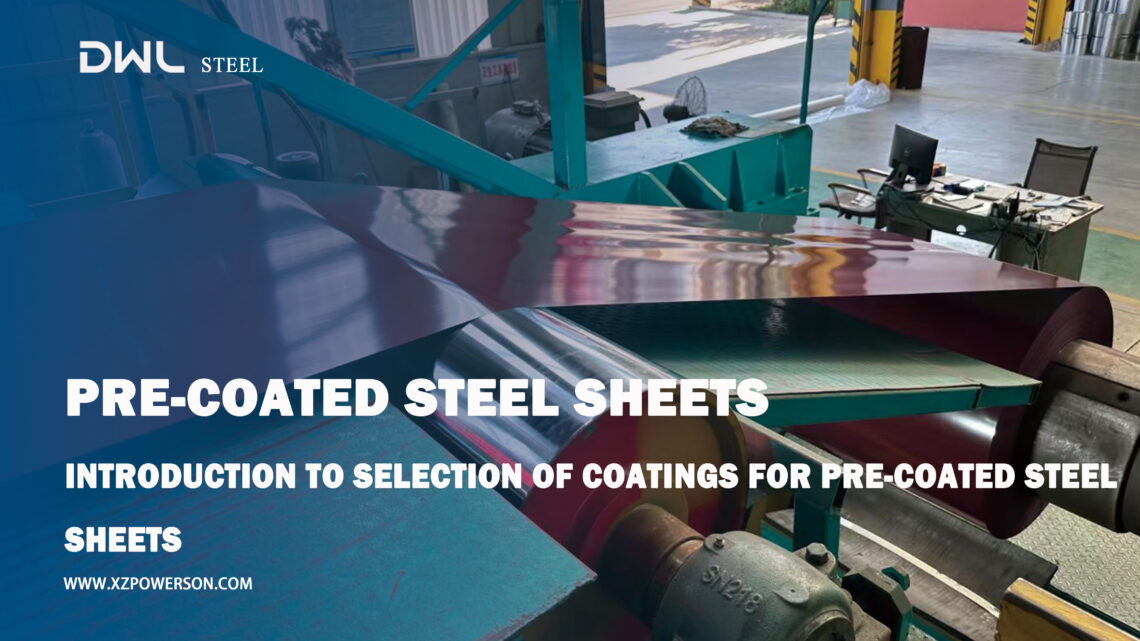
Introduction to Selection of Coatings for Pre-coated Steel Sheets
Introduction to Selection of Coatings for Pre-coated Steel Sheets
(Color Coated Steel)Pre-coated steel sheets, commonly known as color coated steel, are fabricated by applying multiple layers of coatings onto metal substrates (primarily galvanized or galvalume steel) followed by baking. The surface coating not only imparts aesthetic appeal but also endows the product with resistance against environmental degradation. Hence, the judicious selection of coating types and qualities is pivotal to enhancing product performance.
Overview of Coating Types
Color coated steel coatings can be broadly categorized into four major types: polyester (PE), silicone-modified polyester (SMP), high-durability polyester (HDP), and fluorocarbon (PVDF), each tailored for specific applications:
•Polyester (PE) Coatings: Economical with a wide color range, they offer good mechanical properties and workability, suitable for indoor use or mild outdoor environments.
•Silicone-Modified Polyester (SMP) Coatings: Provide enhanced weather resistance and UV protection compared to PE, fitting for moderately corrosive outdoor conditions.
•High-Durability Polyester (HDP) Coatings: Boast superior weatherability and color retention, effectively withstanding exposure to the elements, ideal for extended outdoor usage.
•Fluorocarbon (PVDF) Coatings: The premium choice, offering exceptional weathering properties, chemical corrosion resistance, and extended lifespan, best suited for harsh climates and demanding environments, albeit at a higher cost.
Environmental Factors ConsiderationsWhen selecting coatings, careful assessment of the specific usage environment is essential, encompassing factors such as:
•Climate conditions: In areas with high humidity, salt spray, or intense UV radiation, HDP or PVDF coatings with heightened durability are recommended.
•Pollution levels: For industrial zones or regions with poor air quality, PVDF coatings are preferred for their superior chemical corrosion resistance.
•Application purpose: Roofing materials necessitate focus on weather resistance and waterproofing, whereas appliances prioritize aesthetics and safety.
Functional Requirements
Depending on the specific application of the color coated steel, coatings with specialized functions may also be required, including:
•Antibacterial and mold-resistant: In hygiene-critical settings like food processing or medical facilities.
•Self-cleaning: Through special processes that create a microstructured surface, enabling self-cleansing through rainwater.
•Insulation: Incorporating coatings that reflect infrared radiation, reducing energy consumption in buildings.
Economic AnalysisWhile high-performance coatings like PVDF demonstrate greater long-term cost-effectiveness, they entail higher initial investments. Therefore, it’s crucial to strike a balance between fulfilling functional requirements and optimizing cost-effectiveness based on a comprehensive analysis.
ConclusionIn
Conclusion, selecting coatings for color coated steel involves a multifaceted decision-making process, incorporating material science, environmental considerations, and economic planning. By accurately assessing the usage environment, defining functional needs, and conducting an economic analysis, one can ensure the selected coating not only meets practical requirements but also achieves an optimal balance between economy and durability. Close collaboration with professional suppliers is advisable when procuring and applying color coated steel to obtain the most suitable coating solution.
After the successful development of zinc-aluminum-magnesium products domestically, claims emerged that “zinc-aluminum-magnesium will completely replace galvanization within three to five years.” This led numerous enterprises to consider establishing zinc-aluminum-magnesium production lines or converting their existing galvanization lines. But which direction is the actual situation likely to take?
Looking abroad for perspective, Japan, as the pioneer in researching and producing ‘medium aluminum’ zinc-aluminum-magnesium and the largest user in coastal construction, has exhibited growth in its zinc-aluminum-magnesium capacity as previously graphed. Europe, on the other hand, was the first region to study and produce low-aluminum zinc-aluminum-magnesium, with the highest application in automotive sheets, and similarly, its zinc-aluminum-magnesium capacity growth trend mirrors that of Japan’s.
Both statistical graphs indicate a steady, rather than exponential, increase in zinc-aluminum-magnesium production capacity, with recent signs of slowing growth. Typically, a product intended for full substitution would demonstrate an exponential growth curve with accelerating speed. Hence, from the standpoint of mature markets, the growth potential for zinc-aluminum-magnesium appears limited.
Comprehensively analyzing this, we conclude that zinc-aluminum-magnesium serves more as an improved version of galvanized products rather than a direct replacement. It is unlikely to fully substitute galvanized steel. In the future, zinc-aluminum-magnesium, as part of the thermally galvanized coating series, will hold a competitive position alongside products like aluminum-zinc-silicon and electroplated aluminum-silicon, finding specialized applications where it can exhibit unique advantages.
The market exploration, cultivation, and promotion of zinc-aluminum-magnesium products require further concerted efforts. Exporting zinc-aluminum-magnesium products to avoid taxes may not prove a sustainable strategy.
Nationwide, some companies that have started production have not witnessed the explosive market growth they anticipated, with room for improvement in product quality. Some have ceased production, while others are eager to enter the market. The outlook for zinc-aluminum-magnesium coated products should neither be over-hyped nor ignored but approached with scientific analysis and rational decision-making.
The advent and development of zinc-aluminum-magnesium enriches the continuous hot-dip coating product portfolio. Continuous hot-dip galvanizing processes, based on galvanization, gain even more vitality in competition against batch hot-dipping and electroplating, contributing significantly to environmental protection and energy conservation.
In summary, while zinc-aluminum-magnesium adds diversity to steel strip continuous hot-dip coatings, it is not positioned to fully displace galvanized products. Its role is complementary, carving out a niche in specific applications where its unique properties can be best utilized.
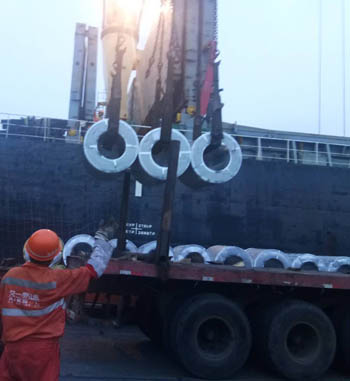
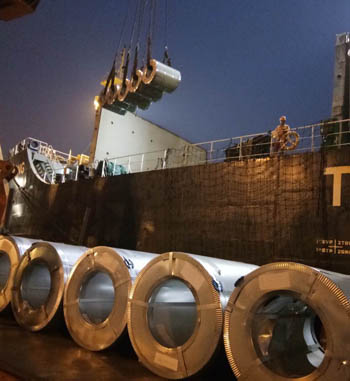
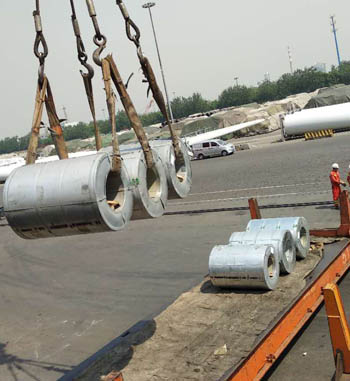
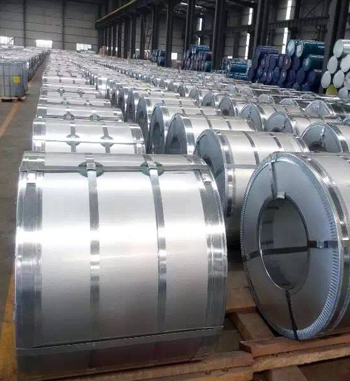
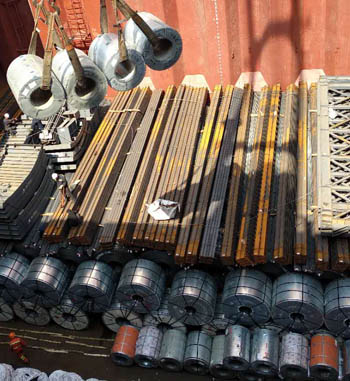
PROFESSIONAL TEAM
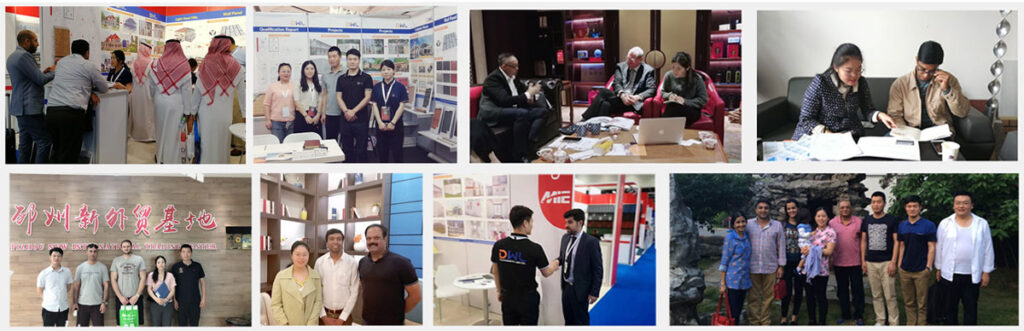
Related Products
21 years steel export experience for Color Coated PPGI